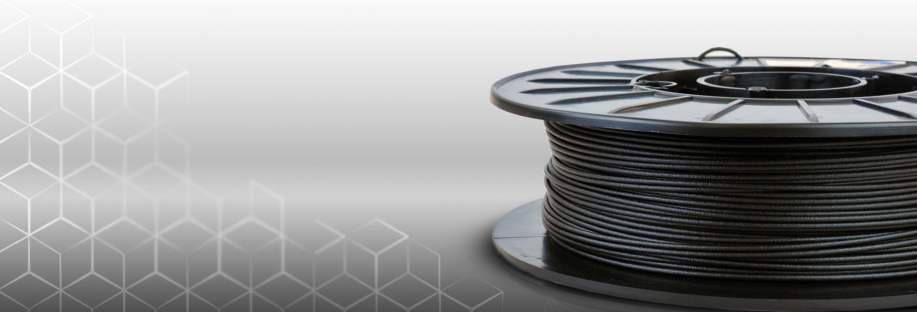
From a lightbulb to space rockets, Carbon Fiber Filaments are taking over and replacing steel and metal parts in various industries. Why? Well, Carbon fiber is five times stronger than steel and at the same time lighter. These characteristics make carbon fiber suitable for applications that depend upon a material’s features to optimize performance, which is especially desirable in the automotive, military, aerospace, and other similar industries.
What are Carbon Fiber Filaments?
Carbon fiber was first discovered in 1860 by Sir Joseph Wilson Swan. Later on, Thomas Edison used cellulose-based carbon fiber material on the first light bulbs that were heated by electricity. Its high heat tolerance made them ideal electrical conductors. Although carbon fiber has been around for over 150 years, is within the late 1970s that new kinds of carbon fiber entered the worldwide market. These newer fibers contain more than 90% carbon and have considerably increased strength-to-weight and stiffness-to-weight ratios. With the assistance of those modern advances, as well as decreases in manufacturing costs we helped fully understand the potential of carbon fiber material.
As most of you probably already know, carbon fibers are rarely used on their own. Usually, we discover them combined with other materials to make a composite material; carbon composites are usually made (beside carbon fiber) of polymer. With this combination, you get a stronger, yet lighter plastic with an increased level of stiffness.
3D printed models that are made of Carbon fiber filament can be used to create many products such as propeller blades, bike frames, aircraft wings, car components, etc.
Carbon fiber filament is formed of carbon fibers, which are mixed with a thermoplastic referred to as the base material. There are plenty of various filaments that can be bought with carbon fiber parts including PETG, PLA, ABS, and Nylon filament. These fibers alone are extremely strong, and after we mix them with the base material we cause the filament to increase in stiffness and strength, and also reduce its overall weight.
The printing parameters of 3D printer for carbon fiber filaments should be similar to those of the base material that the carbon fibers were added to. Since carbon fiber filaments are abrasive and may clog the nozzles of the 3D printer, we recommend using a hardened steel nozzle. Unfortunately not every 3D printer can print with carbon fiber filament because this material requires a high extrusion temperature (at least 230º C) and its abrasive nature can damage brass nozzles (that’s why we recommended the steel nozzle). If you have an FDM printer like Ender 3 V3 SE, don’t worry, with the right Ender 3 upgrades you can print from Nylon Carbon Fiber filament to Flexible filament. You just need to install the Micro Swiss direct drive extruder and use a steel nozzle.
Some companies have developed carbon fiber filaments in an even more technical direction. The base materials of such filaments are high-performance polymers (HPPs) like PEEK. Carbon PEEK is a material with extraordinary characteristics in terms of thermal, mechanical, and chemical resistance. This filament is used in very specific areas where a further increase in mechanical performance is required for an extraordinary performance.
Advantages:
- Good dimensional stability –  the tensile strength of the filament contributes to greater dimensional stability, helping to avoid warping during 3d printing and shrinking.
- Stiffness – Usually polymers that have high strength and durability have lack of stiffness. Carbon fiber doesn’t have this problem, since it has the ability to maintain its shape under high stress. This feature is very desired and used in the automotive industry (as automotive brackets or inspection gauges)
- Overall nice surface finish – Carbon fiber filaments have a nice matt finish. Extremely smooth surface finish allows printability of functional prototypes
- Strength and lightweight –  A formidable tensile strength and lightweight makes carbon fibers ideal for alternatives to metal parts. Low density is the reason why is so lightweight. These features are especially wanted in the robotic industry.
- Heat Deflection – When exposed to heat other materials can deform under pressure or high temperature. Carbon Fiber PAHT filament offers high heat resistance (up to 160 degrees celsius). Carbon Fiber PET is also able to withstand higher temperatures up to 125 degrees celsius. At the same time is it very easy to print this filament.
- Since it has exceptional mechanical properties it can be used for various fixtures, tooling, composite molds for various manufacturing processes, or self-use.
Disadvantages:
- Abrasive filament that wears down brass nozzles. We suggest you use a steel nozzle. Carbon fiber parts don’t melt so be careful the nozzle doesn’t clog. You need to choose the correct nozzle.
- Hygroscopicity – the tendency to absorb moisture. It is very important to have a protected environment for spools of nylon carbon fiber, such as a mylar bag and a sealed material bay.
- Expensive: Due to carbon fiber’s demanding manufacturing processes, the material is known to be more expensive than other filaments like PLA or ABS. This is one of the reasons why it appears in high-end products but not in the mass market.
- Brittle: The combination of polymer and carbon fiber increases the material’s brittleness. The downside of the high stiffness is that carbon fiber can shatter under high impact force or pressure. This means that projects or items that are exposed to such forces are not going to be ideal for carbon fiber.
Where can you use Carbon Fiber?
- We can see carbon fiber being used by high-performance racing teams in Formula 1.
- Aerospace developments have shown that carbon fiber is a  fantastic material for reinforcing wings and bodies of airplanes and are even being tested for next-generation rockets. The lightweight of wings and bodies means more fuel can be carried and longer ranges can be achieved.
- In many sports disciplines like cycling and golf, speed and weight are very important, that’s why companies have dabbled in using composites of carbon fiber to gain a competitive advantage.
- Factories and other manufacturing facilities that use robotics are starting to use carbon fiber to produce tools that can sustain a high degree of force while taking up the minimum amount of the robotic arm’s lift capacity. It can be used for various fixtures, tooling, composite molds for various manufacturing processes, or even self-use.
AzureFilm Carbon Fiber PAHT filament
AzureFilm Carbon Fiber PAHT filament is one of the most popular and the easiest polyamide (PA6) containing carbon fibers to print. The reason why is this material tough, has excellent abrasion resistance, fatigue endurance, good chemical resistance, high strength, and rigidity is because nylon filament itself already possesses the desirable properties. Most manufacturers choose ground fibers since they are cheaper and easier to use. AzureFilm on the other hand uses fibers that are chopped, which means that the tensile strength is higher because the fibers are larger and the product binds more. Besides having excellent tensile and impact strength, Carbon fiber PAHT filament allows short continuous use up to 160°C (Lifetime max. 200h). This filament is fully compatible with soluble supports such as PVA, BVOH, PVOH and fully compatible with breakaway supports such as HIPS. Its water uptake takes about 4 times longer to reach the saturation point compared to unmodified PA6 and it has a saturation point 5 times lower than conventional PA6 materials. The thickness of fibers inside it’s ranging from 0.4mm-0.6mm that’s why we suggest you use the nozzle with a diameter > 0.6mm.
Requirements to work with Carbon Fiber PAHT filament:
- Heated print bed
- Hardened nozzle – Due to its abrasive structure, the filament will wear down the standard brass nozzle over a short period of time. An abrasion-resistant nozzle is required for this type of filament. Since those types of nozzles tend to be less conductive then standard nozzles, usually higher extruder temperatures are recommended
- Heated filament chamber (optional) – Having the filament all the time in a dry place, with working temperature is an optional thing to ensure a consistently controlled environment for the best product quality
- Closed environment (optional) – Ensuring a consistent controlled environment is a very important factor that allows better end class quality of the product although this filament has the ability to be 3D printed on non-heated chamber machines
Printing Recommendations:
- Nozzle temperature: 270 – 290°C
- Heated bed: recommended 90-120°C
- Print speed: 40 – 60mm/s
- Layer height: 0,2mm
- Nozzle dimension: 0,6mm
- Build platform: Blue tape, Kapton tape, glass plate + Dimafix spray
  Â
AzureFilm Carbon Fiber PET filament
The other option AzureFilm has prepared for you is Carbon Fiber PET filament. This material is the easiest filament with carbon fibers to print. Our PET CF has a chopped carbon fiber reinforced structure thus making its impact toughness much stronger. This chopped carbon fiber composite is pushing existing efforts and limitations for research of an engineering-grade 3D printing filament to new frontiers. Filament has excellent mechanical properties with no warping including extremely high z-layer strength and low water uptake. Our Carbon Fiber PET filament is filled with 15% of carbon fiber and has a short-term (max. 3hrs) maximum temperature of up to 125°C. It can easily sustain at 100°C for 10hrs or more. The thickness of fibers inside it’s ranging from 0.4mm-0.6mm that’s why the nozzle diameter has to be 0.6mm.
Fiber-reinforced materials offer exceptional mechanical properties. In addition to typical composite driving factors such as fiber volume and fiber orientation, Â scientists have found out that printing parameters such as nozzle type and speed, Â infill density, layer thickness, bed temperatures, infill pattern has shown to influence mechanical properties.
Significant advantages of AzureFilm Carbon Fiber PET filament:
- Cost-effective – since we are using chopped-up carbon fibers there is a significant reduction in production length, allowing us to make our material cost-friendly for any customer
- Higher temperature resistance up to 125°C
- More dimensional stability – Chopped carbon fibers are extremely strong and not only give high strength and stiffness but also help prevent shrinking as the part is in the cooling down faze
Requirements to work with Carbon Fiber PET filament:
- Heated print bed
- Hardened nozzle – Due to its abrasive structure, the filament will wear down the standard brass nozzle over a short period of time. An abrasion-resistant nozzle is required for this type of filament. Since those types of nozzles tend to be less
- conductive than standard nozzles, we suggest you print with an extruder for higher temperatures. With the steel nozzle, you can print Carbon Fiber PET filament even on a printer like Ender 3. You just need a nozzle that won’t clog (0,6mm) and that can withstand higher temperatures.
- Heated filament chamber (optional) – Having the filament all the time in a dry place is an optional thing to ensure a consistently controlled environment for the best product quality
- We suggest you use a closed environment /printer which ensures a more stable environment, but it is not necessary.
Printing Recommendations:
- Nozzle temperature: 245 – 270°C
- Heated bed: recommended 80-90°C
- Print speed: 40 –60mm/s
- Layer height: 0,2mm
- Nozzle diameter: 0,6mm
- Build platform: Blue tape, Kapton tape, glass plate + Dimafix spray