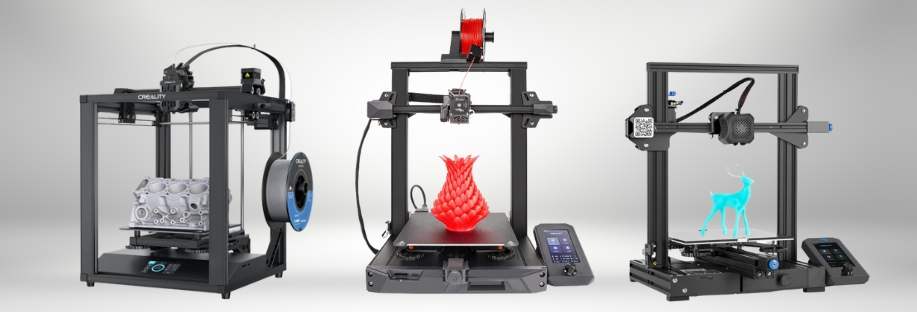
FDM technology is very popular in numerous industries. In this article on FDM printing: What is FDM, we are going to break down what is FDM, how it works, its components, and compatible filaments. We will also discuss the step-by-step process, its benefits and drawbacks, common issues, and how to troubleshoot them. So read the article thoroughly to discover the ways to improve your prints.
Introduction to FDM printing
FDM is the most widely used technology in most industries and has the largest number of 3D printers worldwide. It is probably the first process you think of when you hear the term “3D printing.”
What is FDM printing?
Fused Deposition Modeling is a process where objects are made by adding layers of material, one on top of the other. Thermoplastic filaments are needed in this process. The filament is fed into the extruder which in turn puts it where it needs to go in each layer to make a model or a print.
FDM printing uses a fundamental method called additive manufacturing (AM). This method is the exact opposite of traditional manufacturing, which is subtractive and involves cutting away pieces of a block of material to make a print.
Understanding the FDM process
The working mechanism of FDM printing is simple. It works by layering successively the molten filament fed through the extruder right on the build platform till it forms a print part. But first, you need to insert a design file for the print so the FDM machine can convert it to physical dimensions.
When the design is in place, the next thing is to put a filament spool into the printer. Once the nozzle has reached the appropriate temperature, the printer feeds the filament through an extrusion head and nozzle.
This extrusion head is connected to a three-axis device. This is how it moves along the X, Y, and Z axes. The printer pushes out tiny strands of molten filament and puts them down layer by layer along a path set by the design.
Benefits of FDM printing
- It is possible to use complex shapes and cavities with it.
- Rather clean, easy, and office-friendly.
- It is cost-efficient which helps lowering production costs.
- It reduces the manufacturing time so the products get to be on the market faster.
- The thermoplastics used in FDM are stable both mechanically and environmentally.
FDM technology explained
FDM printer components
FDM printers have a few key parts that work together to make the printing process happen. Let’s look at what makes up an FDM printer:
Extruder
The extruder is where the filament goes. It has a cold end to feed filaments and a hotend to melt them. The molten filament then gets driven by a motor to a small nozzle extruding the filament over the print bed in layers to produce 3D models.
Build plate
A build plate is a flat surface where the nozzle deposits filament to create a 3D print. Normally, it is a heated bed that maintains a certain temperature among the layers throughout the printing process for better layer and bed adhesion. Heated beds also lower the risk of warping and can shift from the X to Y axis to adapt to suit the object’s dimensions. So, get the best print plate for quality 3D prints.
Filament
FDM uses industrial-grade thermoplastic such as ABS and PETG made into a long thin thread coiled on a spool. Considering your FDM printer, the diameter of the filament can be around 1.75 mm to 3 mm. Make use of the vibrant filament options and customise them to unlock your creativity.
Control system
The control system of an FDM printer oversees the printing procedure. It has a microcontroller that translates commands from the sliced model, controls the print bed and extruder temperature, and regulates how the motors move all the while monitoring other set parameters.
Materials used in FDM
Not all kinds of filaments are compatible with FDM printers. Here is a list of common industrial-grade filaments most compatible with FDM printers.
Common filament types
PLA
Polylactic Acid AKA PLA is one of the most used FDM filaments thanks to its low warping percentage, ease of printing, glossy finish, and minimum release of odour throughout the printing process. Manufacturers use sugarcane and cornstarch as raw materials for PLA. This filament comes with an array of vibrant colours for printing models and prototypes.
ABS
Acrylonitrile Butadiene Styrene is an industrial-grade thermoplastic known for its durability, higher heat, and impact resistance. You must use a heated bed for ABS to lower warping and post-processed techniques to make the prints shiny. The filament is a popular choice for printing functional components, electric enclosures, and automotive parts.
PETG
Another FDM-compatible filament is PETG which includes the benefits of both PLA and ABS making it strong, durable, and transparent. PETG has a high chemical and impact resistance which is why it is a proffered choice in making medical equipment, display models, food containers, bottles, and many more.
FLEXIBLE
Flexible is mainly used in making gaskets, phone cases, and footwear due to its flexible and shock absorption characteristics. It includes the properties of rubber but its level of hardness differs from tough to rigid and elastic to soft.
ASA
ASA is a modified form of ABS with a lot of similar properties but comes with better UV, impact, and weather resistance. It has better chemical and heat resistance along with great mechanical strength thus good for printing functional parts, automotive parts, outdoor applications, signage, and more.
FDM printing process step-by-step
In this section, we are going to explain step by step the process of FDM printing for producing high-quality 3D prints.
Preparing the 3D model
First of all, you need a 3D model and this is where most people make mistakes resulting in a poor-quality 3D print. Keep in mind two things explained below to save your print.
Design considerations
In terms of model designing people often make some common mistakes such as using unnecessary support structures without orientation which in turn means time and filament wastage. If the wall thickness isn’t precise, the print becomes fragile. So, remember the following design considerations before printing.
- Reduce overhangs with gradual angles
- Give moving parts appropriate clearances and tolerances
- Provide chamfers and fillets
- Control heat dissipation
- Improve layer adhesion
- Use post-processing techniques
- Don’t design anything that crosses the printer’s capability.
Using CAD software for model creation
Use CAD software to create and modify designs. So, familiarize yourself with the software’s tools and interface. Scale the model properly to ensure correct print size and avoid distortion. Explore the 2D drafting tools for drawing the print’s base shape and then change it to a 3D model. Utilize the software for details. Add features to the design and modify its dimensions. Go to the analysis tool and check for errors and make adjustments. Choose the right file format to save the model and transfer it to the slicer. Define the parameters for the print to get G-codes and upload them into the printer to start printing.
Now you need to frequently check up on the print and resolve issues if necessary.
Slicing the model
Now that you have the model it’s time to slice it with Slicer Software. This software estimates the required filament quantity and calculates the route for producing the print.
Slicer software overview
A slicer as the name suggests thinly slices (0.1-0.3 millimetres) the 3D model in layers. The software generates G-codes or a long list of instructions defining the route for the extruder. According to the instructions, the extruder extrudes filament in layers to create the print. The slicer also estimates the required infill density, temperature, and print speed.
Adjusting slicer settings
For making some adjustments, just open the software and edit the set parameters. While you are on it, think about your preferred print quality, the particularities of the model, and the properties of the filament. Do some experiments till you find the right settings.
Loading filament and calibrating the printer
Filament loading procedures
Read the manual of the printer. Preheat the printer and clean-cut the ends of the filament before feeding it through the cold end. At this point, the filament melts and flows to the nozzle after reaching the extruder.
Bed levelling and nozzle calibration
Use a levelling tool or a paper sheet to readjust the knobs of the build plate and move it near or farther from the nozzle. You have to repeat this process for all the points of the plate to ensure the nozzle is levelled correctly. For nozzle calibration, check the nozzle clearance at different sides of the build plate.
Initiating the print
If all the instructions are in place, you can initiate the printing and for that do the following.
Sending the print job to the printer
Transfer the G-codes to the printer using network connectivity or an SD card and choose the file of the model to start printing.
Monitoring the print progress
You need to monitor the whole process actively as issues such as warping, bad layer adhesion or filament jams are common at this print. So, if this happens make necessary adjustments to get quality prints.
Advantages of FDM printing
FDM printing has a lot of benefits in different sectors. In this section, we are going to discuss the advantages that come with this technology.
Versatility and a wide range of applications
FDM comes with varied applications from prototyping to researching. Now we will look into some of these applications below.
Prototyping
FDM allows for quick turnaround times, enabling rapid iteration and fast prototyping of designs. It accelerates the product development cycle and reduces time to market.
Manufacturing and production
FDM technology eliminates the production issues of traditional manufacturing and promotes faster prototyping and the use of complex geometries in designing models.
Education and research
Researchers and students get to envision and create physical models, assess design concepts and make appropriate adjustments with this technology. It is a great learning method as students can get creative with their designs.
Cost-effectiveness and accessibility
Affordability of FDM printers
These printers come in different categories. You can get an entry-level printer for a few hundred pounds and if you want advanced models with the best features, it can cost around 10 thousand or more.
Availability of filaments
ASA, TPU, PLA, and PETG are some of the best filament options for FDM printers are the best thing is they are widely available. Just use a quality filament that complements your design model to get top-notch prints.
Limitations and challenges
Although printing technology has many advantages, we cannot ignore some of its limitations. With some tips and tricks, it’s possible to overcome these limitations. Following are the common challenges people encounter while printing.
Layer lines and surface finish
Rough surface and visible layer lines are the first issues with this type of printing. It degrades print aesthetics.
Minimizing layer lines
To eliminate this issue, use a small nozzle, adjust the print speed and temperature, and lower the layer height. Upgrade the cooling system to reduce warming and improve layer adhesion.
Post-processing techniques
For better surface finish use post-processing techniques like sanding to smoothen the coarseness. To ensure overall smoothness of the print polish with sandpapers. Acetone vapour or similar products work great to give a smooth finish.
Dimensional accuracy and tolerance
It’s important to ensure dimensional accuracy and tolerance to achieve functional prototypes that match your standard. But a few factors may create issues ruining the print and these are:
Factors affecting dimensional accuracy
Mismatched filament diameter, bad cooling system, warping, wrong extruder temperature, and shrinkage can affect the dimensional accuracy of the print. Layer height, print speed, and bad adhesion can also create this problem.
Calibration and fine-tuning
Printer calibration and fine-tuning can help with this problem. Level the print bed for improving layer adhesion and adjust layer height. Readjust the extruder settings to avoid dimensional errors. Check if the flow rate is accurate and calibrate the print speed and temperature.
Overhangs and support structures
Unsupported overhangs can lead to print failure. Excessive support structures while printing an intricate print can lengthen the print time. It can also leave marks making the surface rough.
Dealing with overhangs
Using temporary support structures minimizes this issue. The slicer can create this support or you can add them yourself for decreasing print distortion. After completing the print, you can remove them.
Types of support structures
Support structures come in different types such as tree support to lower filament wastage. This structure is easy to remove too. If the print needs robust support, go for dense support though removing it might be a little difficult. Another type of structure is called custom supports where you can place supports where necessary.
Troubleshooting and tips for successful FDM prints
Common issues and solutions
Printing with FDM technology does include a few problems that are not much different from traditional printing. Among them, the most common issues are:
Warping and bed adhesion problems
These two problems mostly happen when the filament fails to stick if the bed isn’t heated properly or the layer adhesion is poor. The solution is to use a heated bed. Enclosures, rafts, and adhesive aids also help with this issue. Check the print temperature and speed, and always clean the build plate before printing.
Stringing and oozing
The residual filament can also keep on flowing in non-printing moves causing stringing and oozing. The reasons can be a poorly levelled bed, high sprint speed, or too high extruded temperature.
So, calibrate the retraction settings, and regulate the speed and temperature of the print to mitigate the problem.
Filament jams and extrusion issues
If the extruder temperature is wrong, or the filament gets clogged in the nozzle this issue arises. Failing to properly insert the filament can also cause filament jams. To avoid this from happening always clean the nozzle or change it if necessary, use a high-quality filament, and insert it in the right way. Calibrate the print speed and find the right print temperature.
Top tips for optimisation
Print speed and layer height considerations
Problems like warping and stringing happen because the layer height isn’t proper or the printing speed need adjusting. Printing too fast in the case of complex models means compromising design details thus, lower the speed for better detailing. Try running some experimental tests to find the accurate speed.
Thick layers may print faster but it compromises with small details. On the contrary, thinner layers are great for small details though consume too much time. Find a suitable layer height according to your printing needs.
Temperature settings and cooling
Different filaments have different melting points. Thus, some of them print best at high speed and vice versa. Read the filament manual for finding the right temperature. A heated build plate promotes better layer adhesion. So, preheat the bed with the right temperature suited for your filament.
Proper cooling of the layers is crucial to avoid stringing and oozing. Use cooling fans to prevent overheating so the filaments harden faster.
Design considerations
Learn how to choose the right filament as per the design and complexity of the print. The wall thickness should be compatible with the design too. Use support structures if needed and for a smoother surface consider the print orientation.
Frequently Asked Questions
What is an FDM printer?
Fused Deposition Modeling is a modern 3D printing procedure invented in 1989.
What is the difference between FDM and PLA?
FDM is a printing technology whereas PLA is a filament used for making 3D prints.
Why is FDM better?
FDM is an advanced 3D printing process that is fast, affordable, produces quality prints, and is compatible with an array of filament options.
What is an FDM or SLS printer?
FDM stands for Fused Deposition Modeling and SLS stands for Selective Laser Sintering. Both use the same additive manufacturing technology but SLS printers unlike FDM printers use laser to selectively sinter powdered materials instead of molten thermoplastic filaments.
What are the disadvantages of FDM printing?
Rough surface finish, stringing and oozing, warping, and shrinkage are some of the common disadvantages of FDM printing.
What is FDM good for?
The technology offers diverse applications such as jigs and fixtures, prototyping, architectural models, and more.
FDM printing has numerous benefits and it’s tough to incorporate all of them in this article. It has made the printing process much faster, easier, and cost-efficient. It has created a revolution in prototyping and manufacturing.